設計段階
電気・電子設計
電気回路や基板を設計することが、電気・電子設計の主な仕事です。まずは、企画段階で決定した仕様を実現するために必要な部品(ICなど)の選定や、必要に応じてカスタムICの開発を行い、回路図を作成するところから始まりました。
仕様を実現するといってもさまざまな方法がありますので、多くの回路案の中から、性能や信頼性だけでなく、コストも含めて最良・最適になるように回路設計を行っていきました。
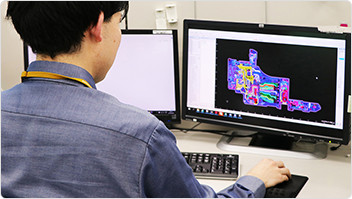
次に、動作するサンプル品をつくって、企画段階で考えたことを実現できているかどうか実験を行いました。たとえば、本体からNintendo Switchドックを経由してテレビへの映像出力を違和感なく行えるかどうか、などです。開発初期にある程度の論理検証をしていても、実際に作ってみるとそのとおりにはいかないケースも多くあります。一度に解決することはできませんので、丹念に課題をひとつひとつ解決して、設計仕様を決めていきました。
機構設計

「目で見えるもの」「手で触るもの」「耳で聞くもの」などの要素を実際の形にしていくことが機構設計の主な仕事です。
その中で「使いやすさ」「壊れにくさ」「組み立てやすさ」「安全性」を考えながら設計(開発)していきます。
設計には3D CADを使用し、デザイナーがデザインした形状を基に基板やさまざまな部品の形状や配置を決めるレイアウト設計に始まり、さまざまな部品や構造を詳細に設計(開発)していきます。
Nintendo Switchでは、限られた空間の中で効率よく冷却する構造を開発した放熱設計、電気的要素を含む液晶・スピーカー・充電池などを回路担当者と共同で開発したモジュール部品設計、外観部品・操作系の機構部品・内部構造部品を開発した筐体設計など、機構設計の仕事は多岐に渡りました。
レイアウト設計
レイアウト設計では製品を構成する部品を各々配置していき、「電気的性能に問題はないか」「使い勝手に問題はないか」などを回路担当者と協力して確認し、作り込んでいきました。ある程度問題がないことが確認できた段階から、デザイナーによる形状のデザインが始まります。
Nintendo Switchでは、一体型のゲーム機を本体部分(液晶・メイン基板)、右コントローラー、左コントローラーに3分割することから始まりました。
限りなくシンプルに見せたい本体部分と、さまざまな機能を詰め込みたいコントローラー部分(Joy-Con)といった役割に応じてこの3アイテムに搭載する機能(部品)をそれぞれ検討し、最大の難関の1つであった本体とコントローラーのドッキング構造を並行して考えていきました。
ドッキング構造に関しては、「快適に取り付け・取り外しができること」「取り付け状態では本体とコントローラーにガタ付きの無い一体感があること」が求められたため、開発担当者間で試行錯誤を繰り返し、数十種類のサンプルを作製しながら最適な構造に絞り込んでいきました。
詳細設計/デザイン検証
詳細設計では、レイアウト設計での検討結果をもとに、実際の商品性を確認しながら細かい部分を仕上げていきます。シミュレーション技術を活用し、強度解析・熱解析・SI※解析を行い、検討結果をもとに基板設計や機構設計およびデザイン検討を進めていきました。
CAD上では確認できない問題点を洗い出すため、3Dプリンターでモックを作製し、電気評価・操作感評価・デザイン性確認・組立性確認を行いました。
この「問題点の洗い出し⇒修正⇒モック確認」といったプロセスを何度も繰り返し、最終仕様(最終形状)に近づけていきました。
※SI = Signal Integrity:信号品質
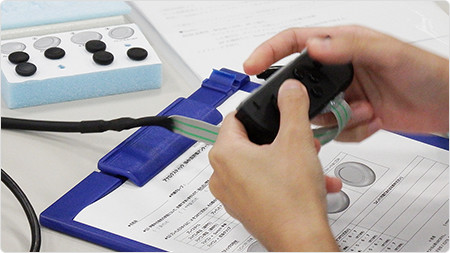
Nintendo SwitchのJoy-Conでは、小さいサイズながらもより良い操作感にしたいとこだわりを持ち、「本体装着状態」「単独状態」「おすそわけ状態」の3スタイルでの操作感を成立させるために、ボタンの配置・感触・高さ・形状に関して、ゲームソフト開発部門と何度もやり取りを重ねて、電気性能・デザイン形状・機構構造を作り込んでいきました。
特に、ゲーム機の肝となるコントローラー部の操作性については、世界中の人々がさまざまなゲームを快適に遊べるようなデザインを反映した実物に近いモックを数えきれないほど作製し、それぞれジャンルの異なるソフトウェア部門のスタッフや海外のスタッフと触って確かめては改善していくといった手法で、何度も検証を重ねました。また、それぞれのボタンを押したり、本体にコントローラーを付け外したりするときの感触や音にもこだわりを持って、設計作業を進めていきました。
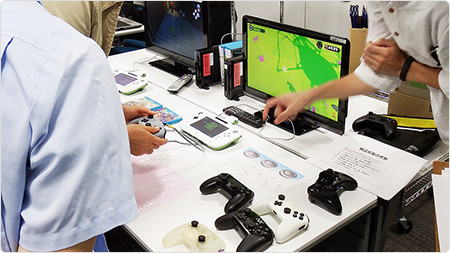
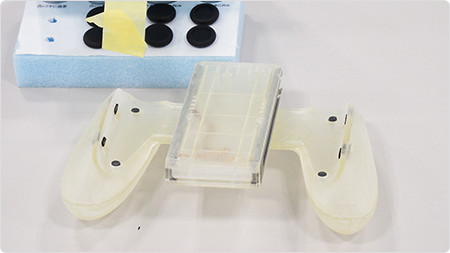
金型作製
詳細設計を経て、各部品ともに最終に近い状態で金型を作製します。金型を作製する理由としては、一度に大量の部品(または部品の一部)を、精度よく作製することができるからです。
しかしながら、金型を作製してしまうと以後大きな変更はできません。大きな変更が入った場合、金型を作り直すことになり、多額な費用と大幅な時間のロスになります。そのため、金型を作製するということは設計(開発)自体も大詰めという証です。
Nintendo Switchでは金型を100種類以上作製しました。
金型を使って作製する部品はプラスチック部品だけではなく、金属部品、液晶の一部の部品、操作スイッチの一部の部品も金型を使って作製しました。
金型が完成した段階で、その部品ひとつひとつに対し、機能(性能)・形状・組立性を事前検証することで、次のフェーズである試作をスムーズに実施できるように準備しました。
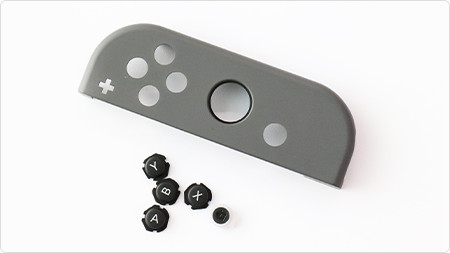
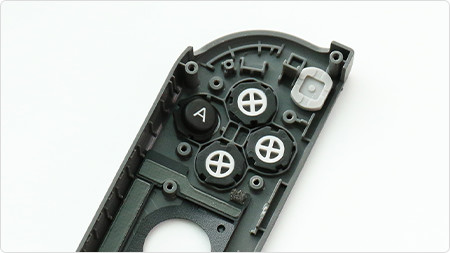
試作・試作検証
試作・試作検証では設計結果をもとに作製した最終形状(最終仕様)に近い部品(金型品)を使用し、試作品を大量に作製します。
その試作品で十分な性能がでるかを確認していきます。どのような使われ方をしてもゲーム機として十分な性能がだせるように、ひとつひとつ調査・検証し、調整および改善をしていきます。
Nintendo Switchドックでは、快適なドックイン/ドックアウトがどの本体・どのドックでも最適に行えるように、コネクターの部品バラつきを確認したり、嵌合(かんごう)の調整を何度も実施したりするなど改善を重ねていきました。
またNintendo Switchの量産にあたっては協力工場が複数あるため、工場ごとの仕上がりのバラつきも予想されました。通常、工場ごとの仕上がりの平均化をすることがとても難しいため、Nintendo Switchでは、それらを考慮した材料の選定や調色についても検証を行いました。
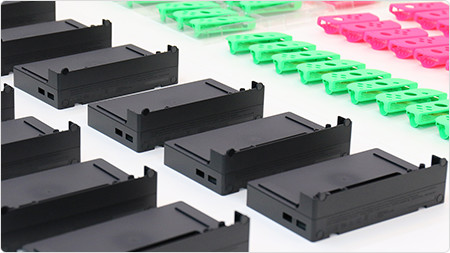
製造段階
1.組立方法の確立
製品設計の段階から開発(設計)部門と協力して
「作業者が組み立て難い箇所」「組み立て間違いを起こしやすい箇所」「作業が自動化できる箇所」などの意見交換を行い、早い段階から設計に反映させることで、組立性の向上や安定した品質を確保できるように努めました。
意見交換する際には、3D CADデータや3Dプリンターで作った簡易モックアップを使い開発部門にフィードバックを行いました。
SwitchのJoy-Conはサイズが小さく、組み立てに苦労しましたが、試作段階で部品配置や治具(じぐ)の調整などを行い、生産性と品質を向上させました。
全世界向けに出荷するゲームカードについては、莫大な数量を高品質かつ安定的に生産できるよう、部品配置・超音波溶着・ラベル貼付(ちょうふ)・トレー梱包の各工程を自動化しました。
製品設計と並行して自動設備の設計開発を進めていましたが、当時は製品の設計検討段階で仕様が未確定な状況であったため、製品仕様が変更となるたびに製造設備への影響がないかを都度設備メーカーと調整を行いました。
具体例としては、成形品の形状でのラベル貼付ズレを減らすために、ラベルの厚みやコシの強さの設計変更提案を行い、貼付け精度の向上を行いました。
また、仕様検討段階でカードケースの形状がブックレットタイプへ変更されたため、3DS用カードケースの自動梱包設備の改造を行い、Switchカードケースで使えるようにしました。
2.検査方法の確立
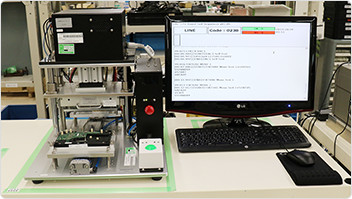
製品の品質を守るために、工程内ではさまざまな検査をしていますが、その中でも特に電気検査では、検査ソフト・ハードの設計を開発試作前段階から開発部門と協力して行いました。
工程で実施する電気検査のうち、基板検査では、基板に電子部品が正しく実装され、機能を満たしているかを確認する検査を実施しますが、その検査器設計において、基板設計の初期段階から検査項目や必要TP(テストポイント)の配置について、開発部門と一緒に検討しました。
ほかにも、複数の協力会社での量産立ち上げや作業者の省人化を目的とした、Nintendo Switch本体およびJoy-Conの各種基板検査の自動化を行いました。
また、Nintendo Switch本体などの製品の品質を向上させるため、継続的に改善努力を行っております。
3.生産工場の管理
Switchの量産は、本体以外にもJoy-Con・ドック・ストラップなどの周辺機器を含む複数製品をほぼ同時期に複数の協力会社で立ち上げたため、過去にはなかった大変さがありました。
たとえば、本体セットに含まれるアイテムのうち、たったひとつの製品が納期どおりに工場に届かなかったり、納品された部品に不具合があったりした場合は、製品が完成せずに出荷できなくなってしまいます。
また、急な仕様変更により作り直しが発生した場合は、今まで作った製品や部品が出荷できなくなってしまう恐れがあります。
このような問題が起こらないように、海外の部品メーカーや協力会社に直接出向き、
「任天堂が依頼したとおりの製品が作られているか」
「想定した数量ができ上がっているか」
「不具合が混ざっていないように検査が正しく行われているか」
などを確認しました。